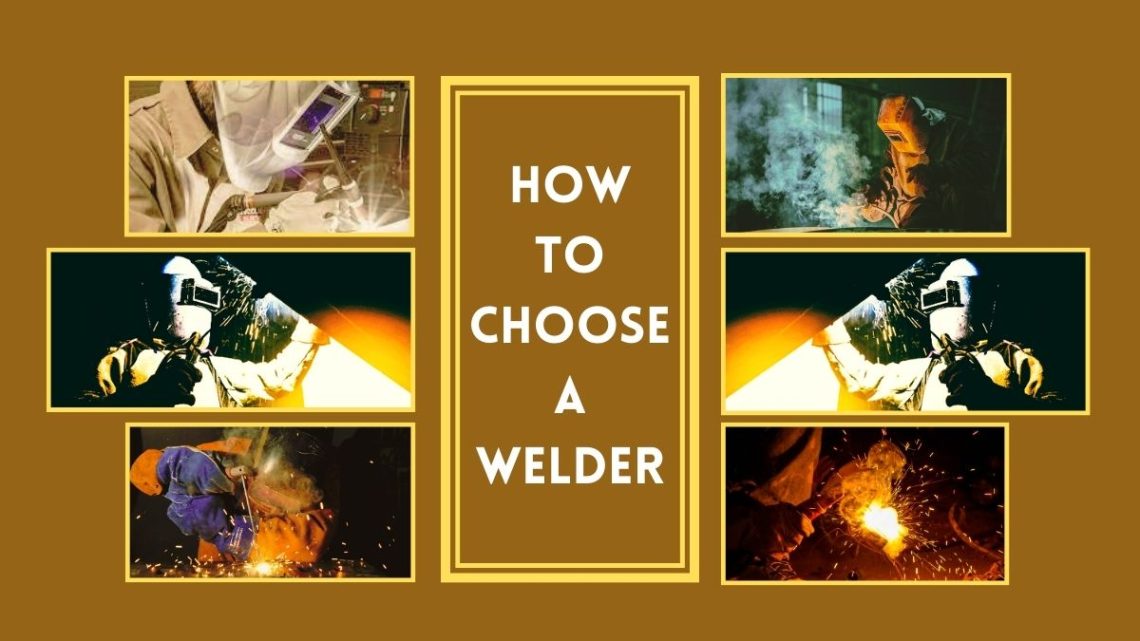
How To Choose A Welder: Expert Tips for Perfect Joining
To choose a welder, assess your project needs and research the welder types available. Consider your skill level, budget, and the materials you’ll be welding. Here, we will discuss how to choose a welder where different expert tips are provided for precise joining.
Selecting the right welder is pivotal for both professional and hobbyist metalwork projects. Your choice should be based on the specific tasks you intend to perform, whether they include delicate, precision work or heavy-duty construction. For beginners, an easy-to-use machine is essential, while experienced welders might look for advanced features and greater versatility.
It’s crucial to balance cost against quality and durability, ensuring your investment enables you to achieve clean, strong welds. The market offers various welding machines, including MIG, TIG, Stick, and Flux-cored, each suited to different welding tasks. Compatibility with the metals you plan to fuse, the welder’s power requirements, and portability also play important roles in your decision-making process. By keeping these factors in mind, you’ll secure a tool that not only meets your immediate needs but also serves you well into the future.
Related Article: Welding Parameters: Tips for Superior Joint Quality
You may also read: How to Weld Galvanized Steel: A Step-by-Step Guide
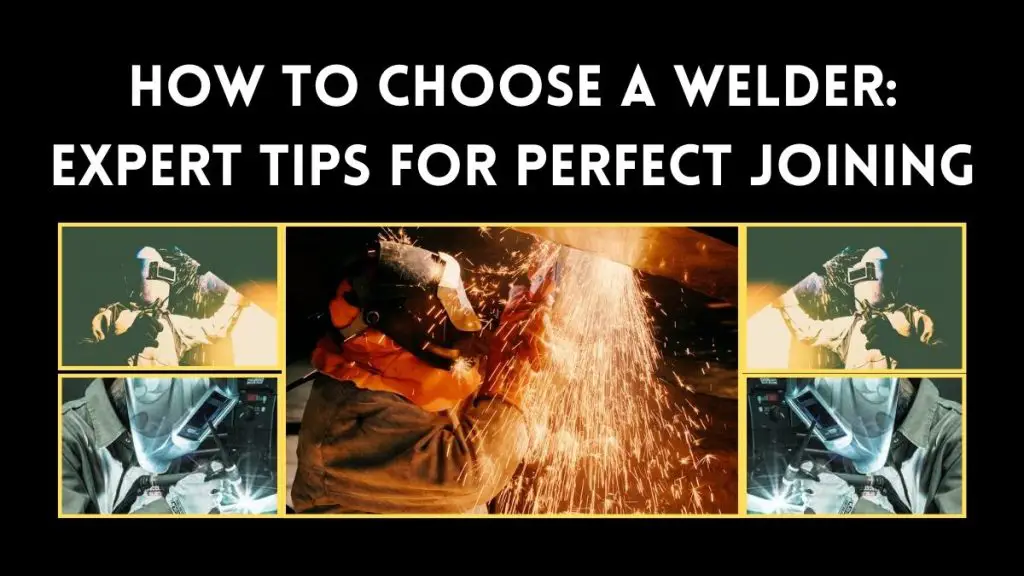
Related Article: The Ultimate Welding Tools for Beginners
You may also read: Is Welding Hard? – The Ultimate Guide to Know about Welding
Essentials Of Welding Technology
Understanding the essentials of welding technology is crucial for those selecting a welder. It shapes not only the outcome but also the safety and efficiency of welding projects. From heat control to metal properties and processes, grasp these fundamentals to make an informed choice.
The Role Of Heat And Metals
Heat is the backbone of welding, with its management being essential for successful joins. Different metals absorb and retain heat in unique ways, impacting the welding process. Resolve to understand these dynamics:
- Melting Points: Metals have varying melting points that dictate the intensity of heat required.
- Conductivity: This influences how heat transfers through the metal.
- Expansion and Contraction: These factors affect how metals cool down and solidify, impacting weld integrity.
Metal Type | Melting Point | Conductivity |
Steel | 1370 – 1510°C | High |
Aluminum | 660°C | Very High |
Copper | 1084°C | Extremely High |
Types Of Welding Processes
Choosing the right welding process is pivotal for a strong weld. We explore different types:
- MIG Welding (Gas Metal Arc Welding): Good for beginners, versatile across metals.
- TIG Welding (Gas Tungsten Arc Welding): Offers precision with cleaner welds, suitable for thin metals.
- Stick Welding (Shielded Metal Arc Welding): Ideal for heavy-duty jobs, works well outdoors.
- Flux-Cored Arc Welding: A mix of the MIG and Stick welding qualities, no need for shielding gas.
Welding Process | Use Case | Skill Level |
MIG | All-around | Beginner |
TIG | Precision tasks | Advanced |
Stick | Outside repairs | Intermediate |
Flux-Cored | Thick materials | Intermediate |
Assess each process to determine which best meets your project’s needs. Factor in metal type, desired finish, and your skill level for optimal results. Armed with this knowledge, you’re closer to selecting the perfect welder.
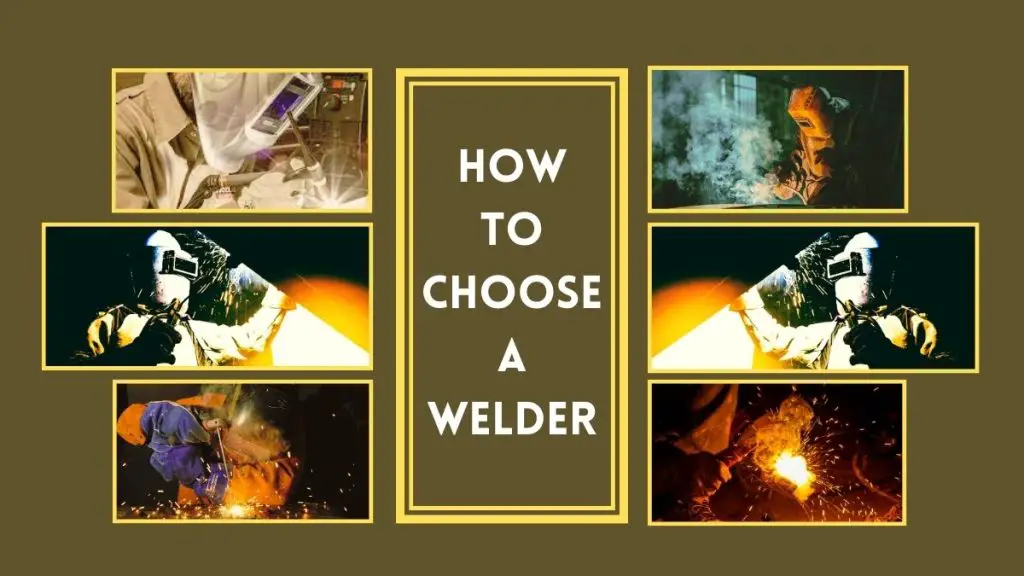
Related Article: The Basics of Resistance Welding – A Complete Guide
You may also read: How to Get a Welding Job: Top Strategies for Success
Identifying Your Welding Needs
Before investing in a welder, it’s crucial to understand one’s unique welding needs. Different tasks demand different types of welders. Identifying specific requirements ensures the selection of a suitable welder who can handle the material and project at hand.
Analyzing Material Compatibility
Selecting the right welder begins with understanding the materials involved. Different welders work best with specific materials. Check material thickness and type before choosing a welding machine. This ensures a strong weld every time.
Use a compatibility chart to match materials with the correct welding process:
Material Type | Welding Process |
Steel | MIG or TIG |
Aluminum | TIG |
Cast Iron | Stick Welding |
Defining The Scope Of Projects
Understanding the project size and frequency is crucial. It dictates the welder’s power and duty cycle needed. For small, occasional repairs, a lightweight portable welder suffices. Larger, more frequent jobs require industrial-grade equipment.
The duty cycle refers to how long a welder can operate without overheating. Take note of the following:
- Short-term projects: A lower duty cycle is acceptable.
- Continuous welding: Look for a higher-duty cycle machine.
Know the project requirements:
- Identify the maximum material thickness.
- Estimate the duration of typical welding tasks.
- Consider power availability and portability needs.
Key Features To Look For In A Welder
Choosing the right welder for your project demands careful consideration of various features. These features determine the welder’s capability and how well it will fit your specific needs. Throughout this post, we will delve into the key attributes you should check before making your selection.
Understanding Power Requirements
Welders require different levels of power based on the tasks at hand. The power output not only affects what materials you can weld, but it also influences the speed and quality of your work. Know the voltage you will have access to and ensure that the welding machine matches it. Additionally, consider the maximum amperage the welder can handle, specifically if you plan to weld thicker materials.
- Input Voltage: Common options include 110/115/120V or 220/225/230V.
- Output Amperage: Higher amperage equals the ability to weld thicker materials.
- Duty Cycle: Time a welder operates at a given amperage before needing to cool down.
Assessing Machine Portability
For those who need to move their welder regularly, weight and size play a huge role in your decision-making process. A portable welder enables flexibility in various working conditions. Look for features like a carrying handle, a compact design, and whether the welder has a wheel kit.
- Weight: Lighter machines are easier to transport.
- Size: Smaller welders save space and are more portable.
- Carrying Handle/Wheel Kit: These additions aid in moving the welder.
Related Article: Top 9 Best Welding Helmets of 2024 for Welding Safely
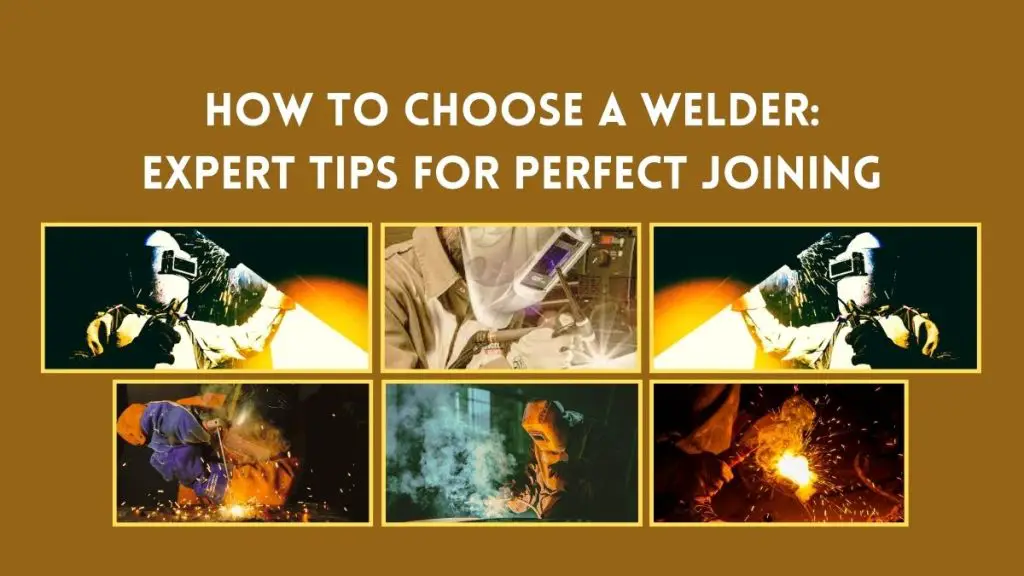
Related Article: The Ultimate Guide to Multi Process Welder
Evaluating Welder Brands And Reviews
Selecting the right welder for your needs involves more than just comparing prices. It is essential to consider the reputation of manufacturers and to scrutinize user reviews. Not all welders fit every job or skill level, so an informed choice requires research and understanding.
Trusted Manufacturers In The Industry
Several brand names stand out in the welding industry:
- Miller Electric – Known for innovation and reliability.
- Lincoln Electric – Offers a wide range, trusted by professionals.
- ESAB – Recognized for versatile welding solutions.
- Hobart – Great for beginners, user-friendly equipment.
These manufacturers have a history of producing quality welding machines. Choosing a model from a reputable brand can assure longevity and support.
Navigating User Experiences And Feedback
Real user reviews provide insight into a welder’s day-to-day performance. Here’s how to sift through feedback:
- Look for consistent comments across multiple reviews.
- Identify whether reviewers mention similar projects to yours.
- Balance professional assessments with honest user opinions.
Review scores and comments on retailer sites, forums, and independent review platforms reveal much about a welder’s capabilities. Pay attention to mentions of durability, ease of use, and customer service experiences.
Remember, a well-reviewed welder by a variety of users offers more confidence than one with limited or single-source feedback. Assure your investment by choosing wisely.
Safety Measures And Best Practices
Embarking on any welding project requires attention to safety. Prioritizing your well-being protects against potential hazards associated with welding. Let’s explore how to secure your workspace with the right gear and maintenance routines.
Investing In Protective Gear
Every welder’s toolkit should start with high-quality protective gear. This gear acts as the first line of defense. Consider these essentials:
- Welding helmet with auto-darkening lens
- Flame-resistant clothing to shield from sparks
- Gloves designed for welding tasks
- Boots that provide both comfort and protection
- Ear protection to block out noise and debris
- Respirators for filtering out harmful fumes
Maintenance Tips For Longevity
To keep your welding equipment in optimal condition, regular maintenance is key. Implement the following best practices:
Equipment | Maintenance Task | Frequency |
Welding Machine | Check and tighten connections | Before each use |
Helmet and Lens | Clean lens; inspect for cracks | Weekly |
Gloves | Inspect for wear; replace if needed | As required |
Work Area | Remove clutter; check for hazards | Daily |
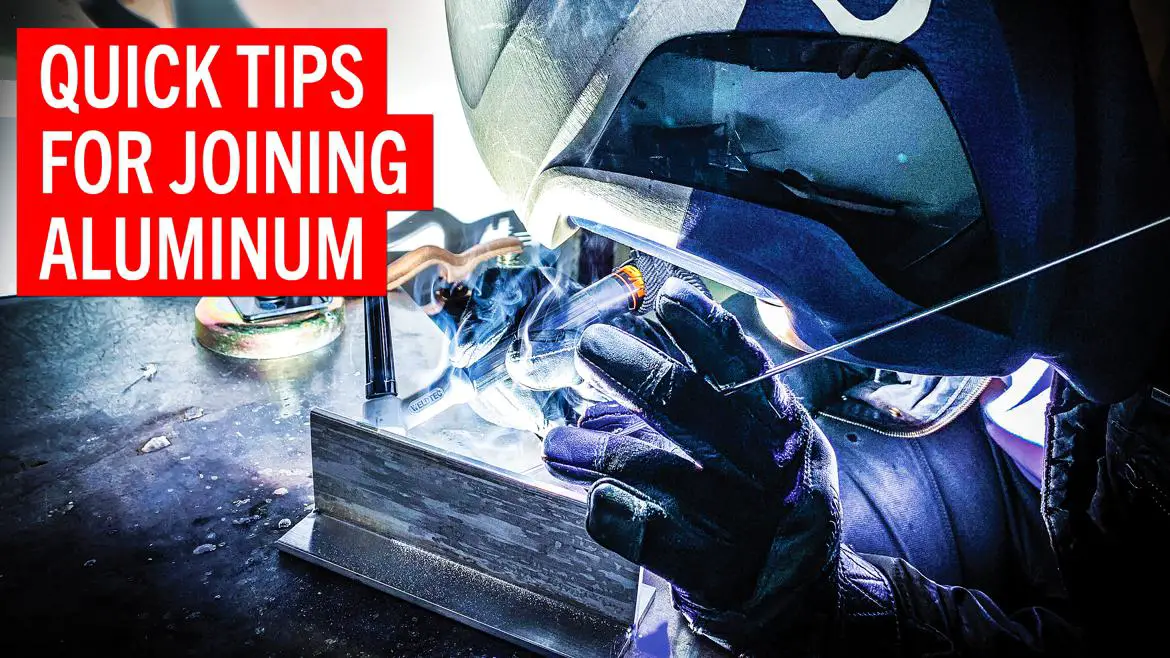
Credit: grassrootsmotorsports.com
Frequently Asked Questions Of How To Choose A Welder
What Factors To Consider When Choosing A Welder?
When selecting a welder, consider the material thickness, welder portability, power supply requirements, and control options. Evaluate the primary material type you’ll be working with and match it to the welder’s capabilities. Ensure the welder can operate within your workspace’s power constraints.
What Welding Process Is Best For Beginners?
For beginners, MIG (Metal Inert Gas) welding is generally recommended due to its ease of use and wide applications. The process is straightforward and versatile, making it ideal for novice welders to start practicing and perfecting their welding skills.
How Does Welder Duty Cycle Impact Performance?
The duty cycle of a welder indicates the amount of time it can operate continuously at a given output without overheating. A longer duty cycle means increased productivity, as the welder can operate longer. Choose a welder with a duty cycle that matches your projected workload.
Can I Use The Same Welder For Different Metals?
Some welders are versatile and can handle various metals, but choosing the right one depends on the specific materials you plan to weld. Multi-process welders are suitable for switching between metals; however, specialty materials may require dedicated welders for optimal results.
To know about Welding Machine Buying Guide>>
Related Article: Top 20 Best Welding Tools of 2024 for Professional Welders
Conclusion
Selecting the right welder is a crucial decision that hinges on the understanding of your project requirements and budget. Opt for a unit that boasts enough power, is compatible with the materials you’re using, and has favorable reviews. Your perfect match in welding equipment is out there; thoughtful consideration will lead you to it.
Remember to prioritize safety and efficiency to ensure a smooth welding experience. Ready, set, weld!
Related Article: The Ultimate Checklist for Welding Safety Equipment
Related Article: How Do Auto-Darkening Welding Helmets Work? – A Complete Guide


5 Comments
Pingback:
Pingback:
Pingback:
Pingback:
Pingback: