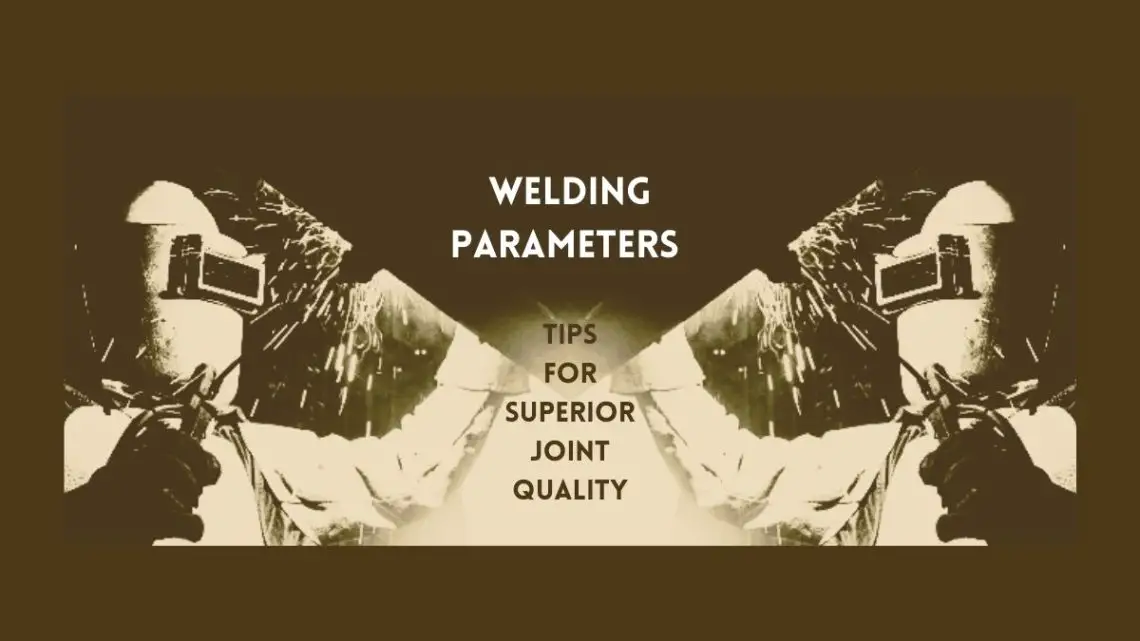
Welding Parameters: Tips for Superior Joint Quality
Welding parameters are critical settings that determine the quality of a weld. These include voltage, current, travel speed, and gas flow rate. Here, we will discuss the welding parameters briefly that would be useful for every welder to maintain the quality.
Understanding the importance of welding parameters is essential for anyone involved in the manufacturing and fabrication industries. These settings directly influence the strength, appearance, and integrity of the weld, impacting the final product’s performance and safety. Proper management of these parameters ensures efficient production and high-quality outcomes, which is why welders must be well-versed in adjusting them according to the material type, thickness, and the specific welding process being used.
Selecting the right combination of these factors can be the difference between a successful project and one that faces structural or safety issues. Knowledge of welding parameters also helps in troubleshooting welding problems and enhances the overall skillset of professional welders, making them invaluable assets in their respective fields.
Related Article: The Ultimate Welding Tools for Beginners
You may also read: How to Get a Welding Job: Top Strategies for Success
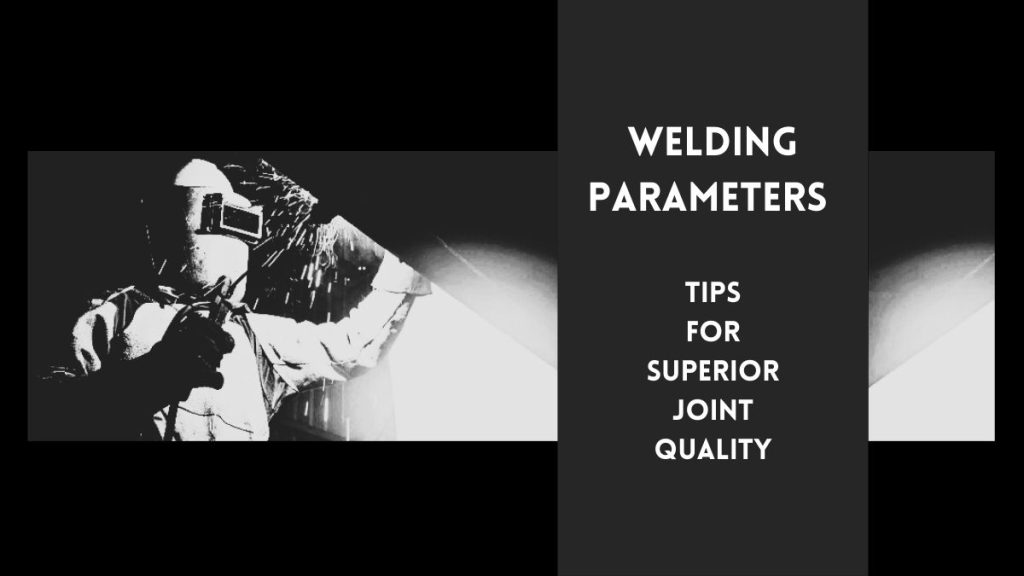
Related Article: The Ultimate Guide to Multi Process Welder
You may also read: The Ultimate Checklist for Welding Safety Equipment
The Essence Of Welding Parameters For Joint Quality
Perfectly joined metals form the backbone of robust structures and reliable machinery. It’s crucial to understand that the strength of these connections largely hinges on the welding parameters used during the process. These parameters act as a recipe for quality, determining how well the joint will perform under stress and over time. Mistakes here can lead to weak bonds that may fail, posing safety risks. Therefore, a deep dive into welding parameters is essential for anyone striving for excellence in metal fabrication.
Key Variables In Welding Processes
Temperature, speed, and technique: these are more than just settings; they are the variables that define the success of a weld. Finding the right balance is a craft, a skill honed by experience and knowledge. Here is a breakdown:
- Amperage: Dictates the heat of the weld.
- Voltage: Influences the arc’s length and shape.
- Travel speed: Affects the weld’s penetration and width.
- Gas flow rate: Shields the process from impurities.
- Electrode: Determines the strength and flexibility of the weld.
- Joint Design: Must match the welding method used.
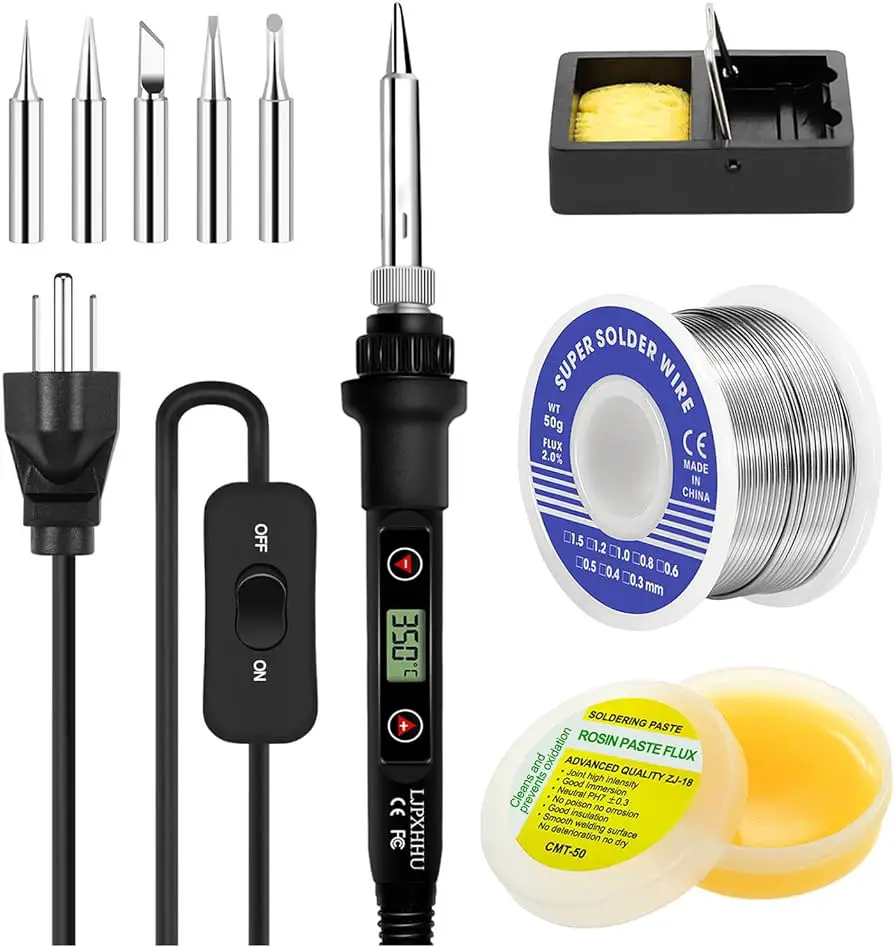
Credit: www.amazon.com
Impact On Strength And Durability
Welding parameters are the architects of a joint’s integrity. Set them right, and a durable, strong bond forms, allowing structures to face the trials of time and pressure. Here’s how:
Parameter | Impact on Joint |
Temperature Control | Ensures proper fusion and prevents defects. |
Consistent Speed | Avoids structural weaknesses by ensuring even coverage. |
Precise Technique | Leads to flawless join with minimal rework. |
Choose wisely; these parameters lay the groundwork for metallic creations that can withstand loads, resist corrosion, and retain their strength through thick and thin.
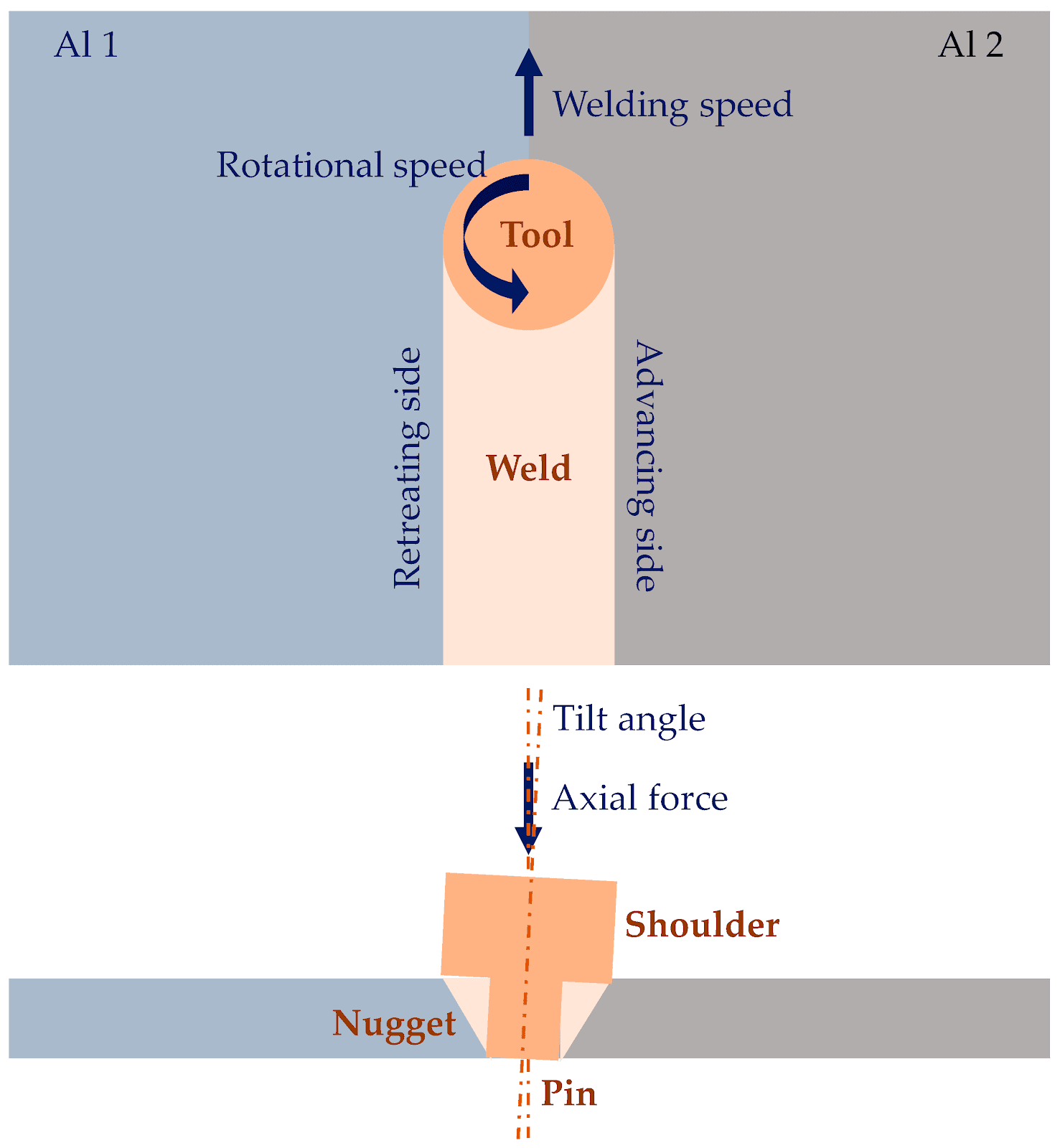
Credit: www.mdpi.com
Optimizing Heat Input For Various Metals
Welders must adjust the heat to join metals perfectly. Different metals need unique heat levels. This balance affects quality. Let’s learn about customizing heat for better welds.
Balancing Penetration And Distortion
Correct heat levels make strong welds with little warping. Here’s what skilled welders do:
- Measure material thickness: Thicker metals need more heat.
- Choose the right power setting on the welding machine.
- Control travel speed: Moving too fast or slow alters heat input.
- Use test pieces to find the perfect balance.
Material-specific Temperature Considerations
Different metals melt at various temperatures. Knowing this ensures good welds. See below:
Metal Type | Melting Range (°F) | Heat Input (kJ/in) |
Aluminum | 1220-1220 | Low to Medium |
Steel | 2500-2800 | Medium to High |
Stainless Steel | 2550-2790 | Medium |
Always use a welding chart or guidebook for precise numbers.
Related Article: Top 20 Best Welding Tools of 2024 for Professional Welders
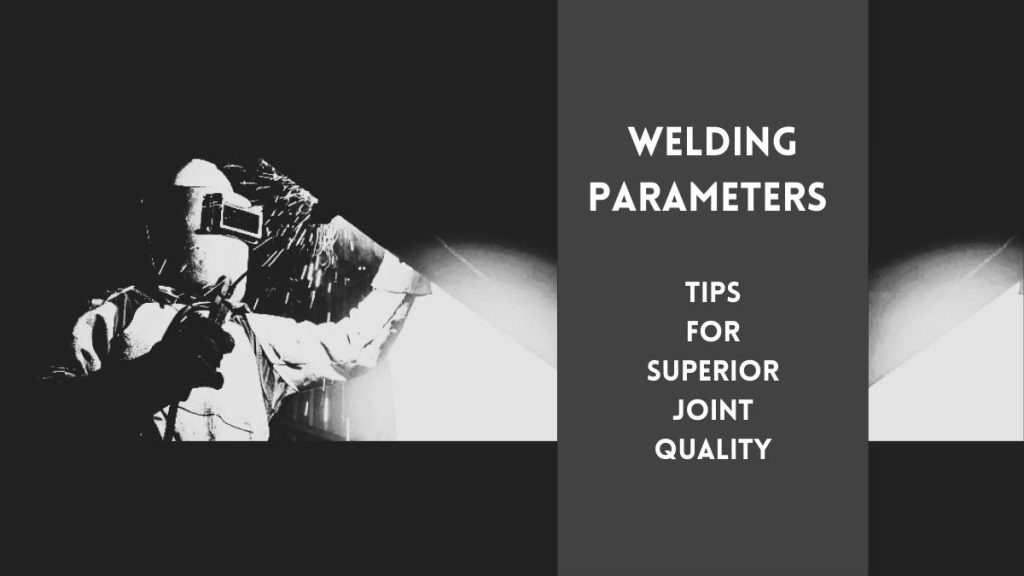
Related Article: Is Welding Hard? – The Ultimate Guide to Know about Welding
Welding Speed And Its Influence On Output
Welding Speed and its Influence on Output is a critical factor in welding operations. It affects both the quality of the weld and productivity. The right speed ensures strong and uniform joints. It also helps to maintain cost efficiency. Balancing speed with quality output is essential for successful welding projects.
Speed Vs. Quality Trade-offs
Welders often face the challenge of balancing speed and quality. Faster welding speeds can boost production rates. Yet, they may lead to defects like porosity or weak joints. On the other hand, slow speeds enhance quality but reduce output.
- Increasing speed can lead to imperfections.
- Reducing speed often improves weld integrity.
- Correct speed achieves a balance between quality and efficiency.
Techniques For Consistent Welding Speed
Maintaining a consistent welding speed is key to quality. Several techniques help achieve this consistency:
- Use a welding positioner to rotate workpieces evenly.
- Implement welding fixtures to hold parts firmly and prevent variance.
- Training welders to maintain a steady hand is crucial.
- Employing automated welding machines guarantees uniform speed.
Digital weld gauges and speed monitoring tools also aid in keeping the speed constant. By using these techniques, welders can ensure a consistent quality output while optimizing speed.
The Role Of Shielding Gas Composition
Welding excellence hinges on numerous variables. Among them, shielding gas composition takes a pivotal role. The right mixture determines the strength, appearance, and durability of the weld. Mastering the subtle art of proper shielding gas selection elevates welding quality to new heights.
Selecting The Right Gas Mixture
Welders face a buffet of gas options. The mix they choose shapes their work. Some popular gases are:
- Argon: Ideal for tight seams and thin metals
- Carbon Dioxide: Cost-effective but can cause spatter
- Helium: Ups heat input for thick pieces
- Oxygen: Adds punch to the welding arc
Combination is key. Mixture ratios influence penetration, arc stability, and welding speed. Balancing these factors is an art. Gas suppliers or welding experts are the best guides for picking the perfect potion.
Controlling Atmospheric Contamination
Even a drop of unwanted gas spells disaster in welding. The shielding gas acts as a guardian, forming an invisible armor against harmful elements. These elements include:
Element | Risk |
Oxygen | Corrosion and weakening |
Hydrogen | Cracks in the weld |
Nitrogen | Brittleness over time |
Consistent monitoring and adjusting gas flow ensure a clean weld pool. Welders use flow meters and regulators for precision. Shielding perfection prevents poor quality welds and safeguards project integrity.
Related Article: Small Welding Projects from Scrap Made Easy: DIY Mastery
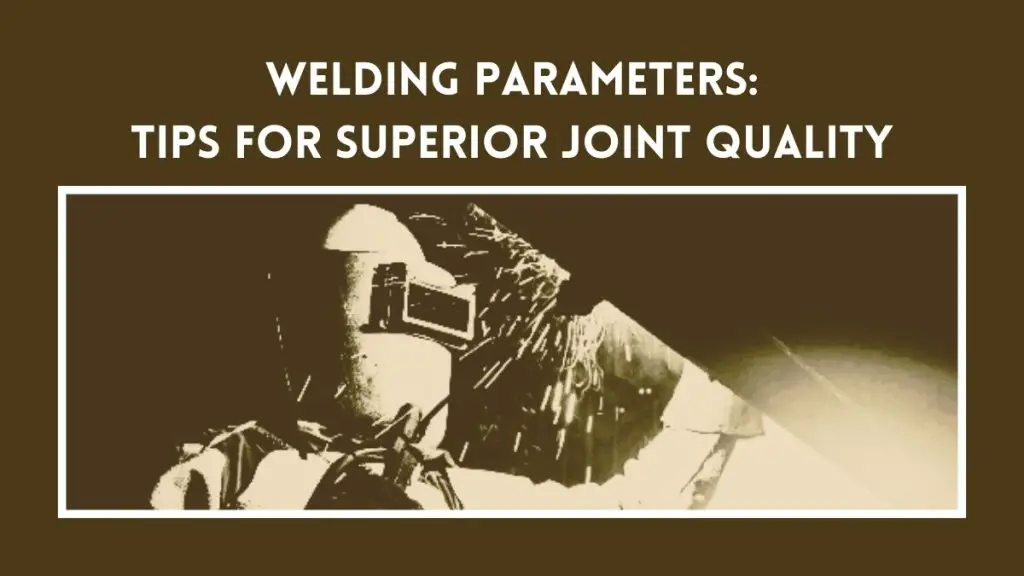
Related Article: The Major Welding Defects You Should Know
Achieving Precision With Welding Techniques
Achieving precision in welding is crucial for creating strong, reliable joints in metalwork. This practice requires meticulous control over various welding parameters. Right settings ensure perfect results. Today’s techniques and technologies make it possible to achieve such precision.
Advanced Methods For Higher Quality Joints
Welders have various advanced methods at their disposal to create high-quality joints. Below are key techniques:
- Pulsed Gas Metal Arc Welding (GMAW-P): Delivers precise control, reduces spatter, and allows for welding thin materials.
- Tungsten Inert Gas (TIG) Welding: Offers clean, high-quality welds, ideal for high-precision fabrications.
- Laser Beam Welding: Provides focused, high-energy welding for precise joints in complex applications.
Each method can be fine-tuned including parameters like:
Parameter | Impact |
Amperage | Determines heat; must match material thickness. |
Voltage | Controls arc length; affects bead width and depth. |
Travel Speed | Influences weld bead quality and penetration. |
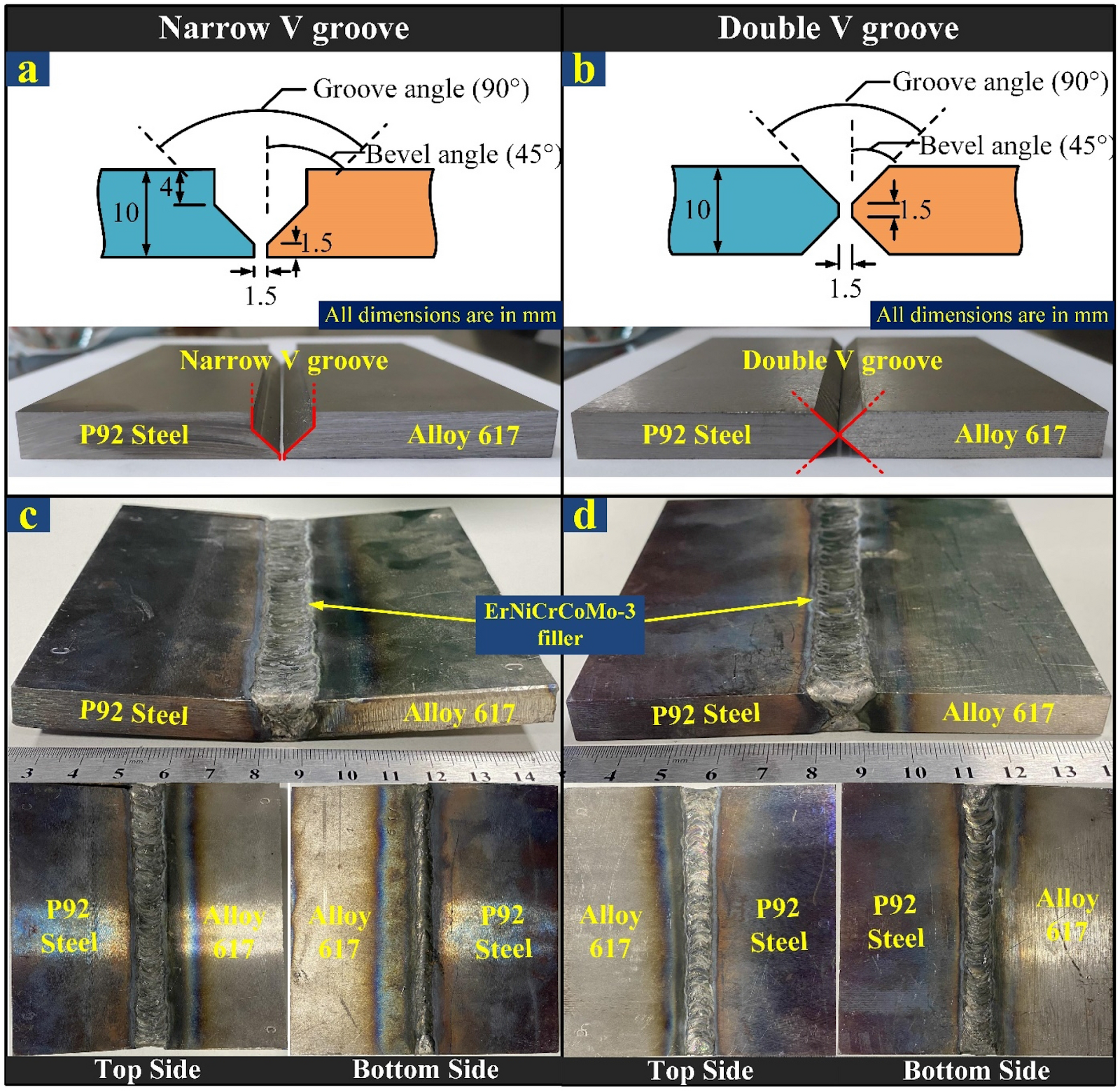
Credit: www.nature.com
Skill Development And Practice Essentials
While equipment and techniques matter, the welder’s skill is paramount. Here’s how to hone your skills:
- Start with base metal prep. Proper cleaning and fitting lead to fewer defects.
- Practice steady hand techniques. Smooth, consistent movements affect weld bead quality.
- Test different positions. Skill in all positions ensures adaptability across projects.
- Experiment with variable parameters. Learn how changes affect the outcome.
- Seek feedback and mentorship. Constructive criticism accelerates improvement.
Becoming adept with various welding techniques demands time and practice. The goal is always a joint that’s as strong as the parent metal. Focus on mastering the control of your welding tools and parameters. Only then can precision in welding be assured.
Related Article: How Do Auto-Darkening Welding Helmets Work? – A Complete Guide
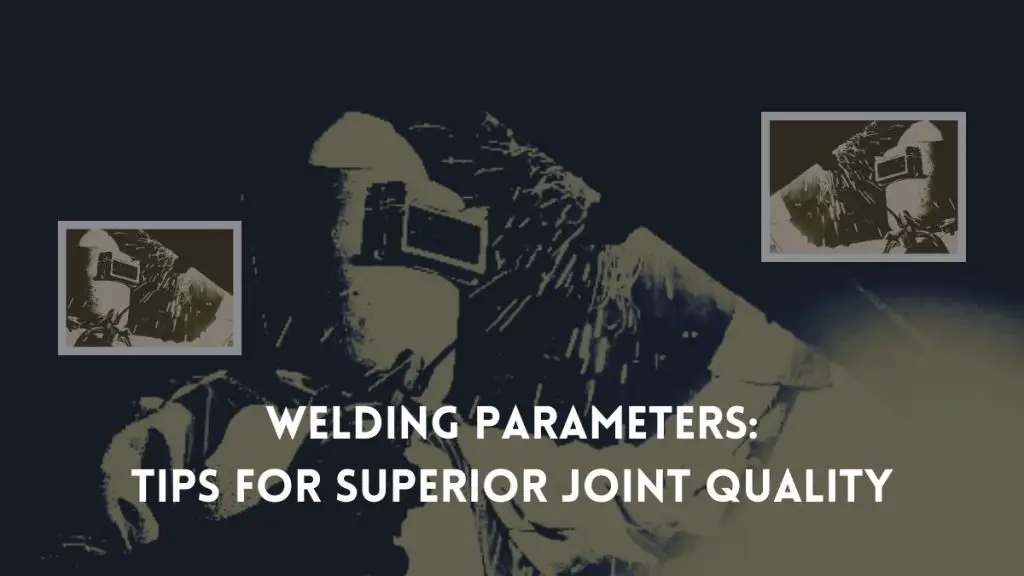
Related Article: Top 9 Best Welding Helmets of 2024 for Welding Safely
Frequently Asked Questions For Welding Parameters
What Are The 5 Welding Parameters?
The five welding parameters are current, voltage, travel speed, arc length, and shielding gas composition.
What Are The Parameters For Welding Quality?
Welding quality parameters include weld seam integrity, correct dimensions, absence of defects, adherence to specified procedures, and appropriate mechanical properties.
What Are The Parameters For MIG Welding?
MIG welding parameters include voltage, wire feed speed, gas flow rate, electrode type, and torch angle. Proper adjustment ensures strong, defect-free welds.
What Are 5 Things Welders Need To Consider In Making A Good Weld?
1. Choose the right electrode for your material. 2. Ensure surfaces are clean and free from contaminants. 3. Set the correct amperage for your welding machine. 4. Maintain a consistent travel speed and angle. 5. Practice proper welding techniques for strong, durable joints.
To know more about Welding Parameters>>
Related Article: How To Choose A Welder: Expert Tips for Perfect Joining
Related Article: The Basics of Resistance Welding – A Complete Guide
Conclusion
Crafting the perfect weld demands precision, understanding, and control over every parameter. From voltage to travel speed, tailoring these elements is crucial for weld strength and integrity. Mastering welding parameters not only enhances outcomes but also ensures safety and efficiency.
Embrace these insights and take your welding projects to the next level.
Related Article: The 9 Best TIG Welders of 2024 for Welding Efficiently
Related Article: Top 7 Best MIG Welders of 2024 for Precise Welding


5 Comments
Pingback:
Pingback:
Pingback:
Pingback:
Pingback: