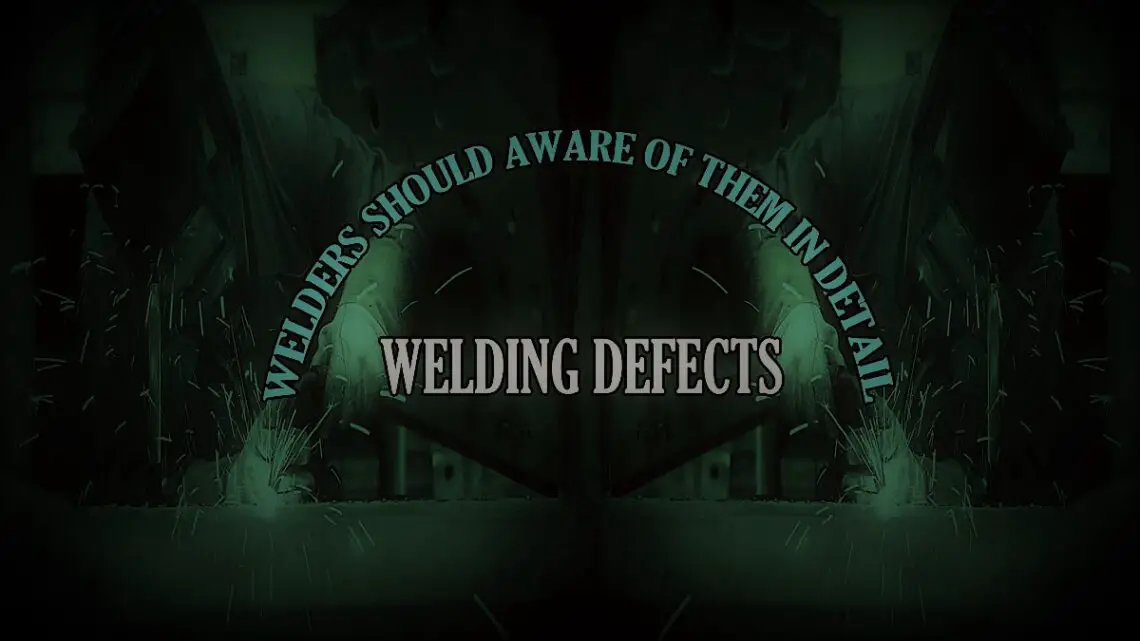
The Major Welding Defects You Should Know
If you are looking for an article about welding defects, then you are exactly in the right place. This welding-related article is all about welding defects which are very essential to know for a welder.
Welding is a common process used in a variety of industries to join two pieces of metal together. While welding is an efficient and safe process, there are potential risks and defects that can arise during the welding process. Some of these defects can lead to serious problems if not addressed timely.
Welding defects can be difficult to detect, especially since they are usually not visible to the naked eye. In order to detect welding defects, welders should use various non-destructive tests. These tests are known as radiography, ultrasonic testing, and dye penetrant testing. These tests will allow welders to detect any problems before they become a major issues.
No matter how experienced a welder is, welding defects can still happen. The best way to prevent welding defects is to use the correct welding parameters, check for proper fit-up, and use non-destructive testing to detect any flaws. By following these steps, welders can ensure that the welds they produce are of the highest quality.
Related Article: Top 9 Best Welding Helmets of 2024 for Welding Safely
You may also read: The Ultimate Welding Tools for Beginners
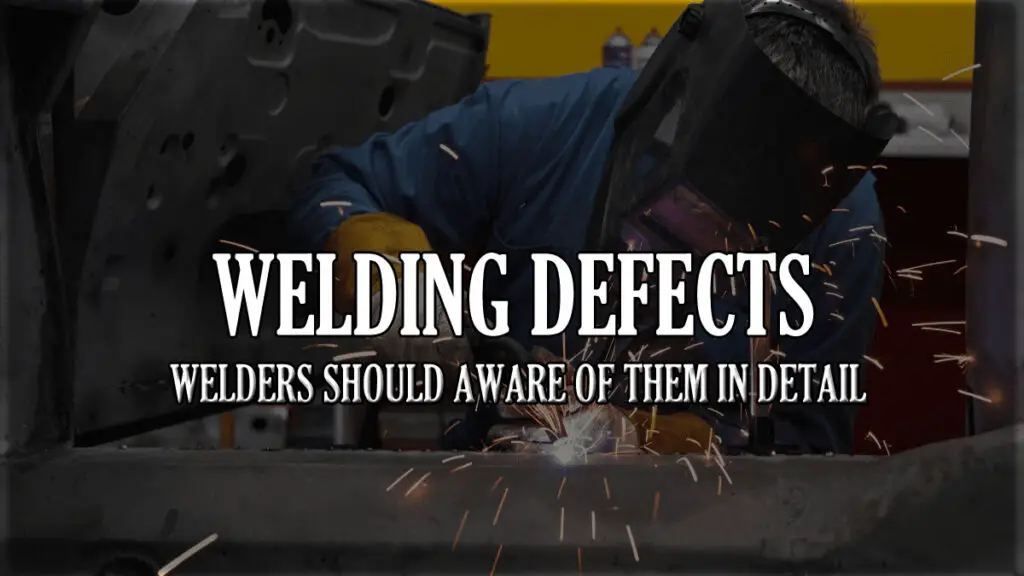
Related Article: Top 7 Best MIG Welders of 2024 for Precise Welding
Related Article: The 9 Best TIG Welders of 2024 for Welding Efficiently
Welding Defects
Welding is a process used to permanently join two metals or thermoplastics together. However, it is not a flawless process and can produce a variety of defects in the finished product. These defects can range from minor flaws to major failures that can compromise the strength and integrity of the weld.
The term “welding defects” refers to the abnormalities created in the metal during the welding process, faulty welding patterns, etc. The flaw could differ from the intended weld bead form, size, and quality. Defects in welding can happen on the exterior or inside of the metal being welded. Some flaws might be permitted if they fall within acceptable bounds, however, flaws like fractures are never allowed.
Common Causes Of Welding Defects
Welding defects occurring by several factors, including poor welding techniques, incorrect fit-up, wrong welding parameters, and improper shielding gas. The most common welding defects are porosity, cracks, and undercutting. Porosity is caused when the weld is exposed to air, or when the welding wire is not clean. Cracks occur when the weld is cooled too quickly, or when there is too much stress in the weld area. Lastly, an undercut is a material loss that results when the weld does not meet the edges of the metal.
One common welding defect is porosity, which is caused when gas bubbles become trapped within the weld. It can weaken the weld and reduce strength and integrity by allowing moisture and other contaminants to penetrate the joint.
Another welding defect is cracking, which can occur for a variety of reasons. It can be caused by excessive welding heat, incorrect welding parameters, or stress during cooling. It can also be caused by the presence of contaminants, such as oxide films, or by undercutting the weld surface.
The presence of inclusions is another common welding defect. Inclusions are bits of foreign material, such as slag, trapped in the weld. This can weaken the weld and reduce its strength and integrity. Inclusions can occur due to improper joint fit-up, insufficient pre-cleaning of the weld area, or use of incorrect welding parameters.
A final welding defect is the spatter, which is caused by the expulsion of molten metal droplets during welding. It occurs by incorrect welding parameters, improper gas shielding, or operating the welding machine at too high of a speed. Spatter can lead to a weakened weld and negatively affect the strength and integrity of the weld.
Types Of Welding Defects
Welding defects can be differentiated mainly into two categories such as exterior defects and internal defects. Here we are discussing both the external and internal welding defects.
External Welding Defects:
Here, we are discussing some external welding defects and their detail :
1. Porosity
Porosity is a common external welding defect that occurs when air or other gases become trapped in a weld. It occurs by a variety of factors, including inadequate cleaning of the base material, incorrect welding parameters, and improper shielding of the weld area. Porosity can significantly reduce the strength and durability of a welded joint, making it a serious concern for welders.
The most common causes of porosity are inadequate cleaning of the base material, incorrect welding parameters, and improper shielding of the weld area. During the welding process, contaminants on the base material can become trapped in the molten weld pool and create pockets of gas bubbles that become trapped in the weld as it solidifies.
Incorrect welding parameters can also lead to porosity. If the welding process is not properly adjusted, the weld may not be able to penetrate the material. It results in shallow welds and pockets of gas that become trapped in the weld. Improper shielding can also create pockets of gas that become trapped in the weld as it solidifies.
To detect porosity, welders should visually inspect the weld area for any signs of gas bubbles on the weld surface. Additionally, welders can use a dye penetrant inspection (DPI) to detect porosity in the weld. This method involves the use of a dye that is applied to the weld. Then it examined for the presence of air pockets.
In order to prevent porosity, welders should take steps to ensure that their welding process is properly adjusted and that the base material is free of contaminants. Additionally, welders should ensure that the welding area is properly shielded with inert gases to prevent contamination from the atmosphere.
2. Weld Crack
Weld cracks are one of the most common external welding defects. It occurs when the weld metal or heat-affected zone (HAZ) forms a crack that is visible from the outside of the weldment. Weld cracks can occur during any stage of welding: from preparation to post-welding heat treatment.
Weld cracks can be caused by a variety of factors, including an improperly prepared base metal, an incorrect welding procedure, incorrect welding parameters, and inadequate weld joint preparation. Additionally, weld cracks can be caused by thermal fatigue and metallurgical stress due to excessive heat input or incorrect filler metal.
When welding cracks are discovered, it’s important to take steps to repair them as soon as possible to prevent further damage. Depending on the severity of the weld crack, the repair process may involve grinding, re-welding, and/or applying filler metal to the affected area. It’s also important to identify the root cause of the weld crack so that it can be addressed to prevent future problems.
3. Undercut
The undercut is a common external welding defect that can have an impact on a weld joint’s strength and performance. Undercut occurs when the weld metal fails to fill the joint, leaving a groove or void along the weld’s edge. It can be caused by a number of factors, including the welding speed, amperage, and welding process. It is important to identify an undercut in welding joints for maintaining the weld’s integrity and performance.
Undercut can occur in any type of welding process, but is most commonly associated with gas-shielded arc welding and metal inert gas welding. These welding processes involve the use of a welding torch and a continuous wire feed. The torch is used to apply heat to the joint, melting the base metal and welding wire together to form a weld. The welding wire then melts and fuses with the base metal to form a bond. However, if the welding speed or amperage is too low, the weld will not properly fill the joint and an undercut will occur.
In addition to inadequate welding speed or amperage, undercut can also be caused by improper joint preparation. If the edges of the joint are not properly prepared, the weld will not be able to properly fill the joint and an undercut will occur. Contamination from oil, grease, dirt and other foreign materials can also lead to an undercut.
The effects of the undercut can be catastrophic. It can lead to a decrease in the strength and integrity of the weld joint, as well as a decrease in the fatigue life of the weld. It can also cause cracking, porosity, and other defects. A visual inspection of the weld joint is the best way to detect undercut, and corrective action should be taken if it is detected.
4. Spatter
Spatter is the term used to describe small droplets of molten material which form during the welding process. The droplets can range in size from just a few millimeters to several centimeters in diameter. Spatter is an external defect that can lead to a variety of problems, including weakened welds and an increase in overall welding time.
Spatter can be caused by a number of factors. One of the most common causes is an incorrect gas flow rate. If the gas flow rate is too high, the gas may not be able to keep up with the arc and will be pushed away from the weld, resulting in a spatter. Poor fit-up of the parts being welded can also cause spatter, as can inadequate shielding gas coverage.
Spatter can create a number of different problems. The spatter droplets can interfere with the welding process, either by blocking the weld or causing a poor-quality weld. The droplets can also interfere with the smoothness of the surface of the weld, resulting in an uneven or rough surface. In some cases, the droplets can even interfere with the corrosion resistance of the welded joint, leading to premature failure.
The best way to avoid spatter is to ensure that the welding process is properly set up. The welding machine should be set up so that the gas flow rate is correct and the gas is able to keep up with the arc. The fit-up of the parts should also be checked to make sure that they are properly aligned and have adequate clearance. Finally, sufficient shielding gas coverage should be ensured in order to minimize spatter.
5. Crater
External welding defects refer to any type of imperfection that appears on the surface of a welded item. These types of defects can cause a variety of problems, ranging from aesthetic issues to structural integrity issues. One of the most common is the crater, a hole or depression at the end of a weld at the termination point. A crater usually leads to weak welds and decreased structural integrity of the welded joint.
Craters can be caused by an improper welding technique, incorrect welding parameters, or contamination at the weld joint. The most common cause of crater formation is poor weld technique. When a welding arc is terminated too quickly, the molten metal is not completely expelled from the weld joint and is instead left behind in the form of a crater. This is because the arc must be maintained in order to expel the molten metal from the joint.
In order to prevent craters from appearing, welders must be aware of their weld technique and the correct welding parameters. Additionally, the weld joint must be free from contaminants, such as rust, paint, oil, or dirt. If the weld joint is contaminated, this can cause the molten metal to stick to the joint, forming a crater at the end of the weld.
Craters can significantly reduce the structural integrity of the welded joint. As such, it is important for welders to be aware of the potential for crater formation. Welders can reduce the risk of crater formation by following the correct parameters and ensuring the weld joint is free of contaminants and ensuring that their welds are strong and reliable.
6. Overlap
Overlap welding defects occur when two metal pieces are fused together. There is a thicker layer of weld metal in the joint. It occurs by the heat of the welding rod or wire melting metal from the base metal of the joint and merging it with the weld metal. The result is an unevenly shaped joint. If not caught in time, will lead to structural weakness and other safety issues.
In order to prevent overlap welding defects, it is important to use the right welding technique and materials. This includes using the right welding rod or wire, the best heat settings, and the correct welding speed. It is also important to make sure that the two pieces of metal being joined together are properly aligned and positioned relative to each other. If the pieces are not properly aligned, it causes the weld to be uneven or too thick in certain areas.
It is also important to inspect the welds regularly and make sure that there is no overlap or other defects. If any defects are found, it is best to repair them as soon as possible. In order to prevent any potential safety hazards or structural issues it is essential.
In some cases, overlap welding defects can be fixed with a re-welding process. This involves removing the defective metal and then welding the new metal in its place. This process can be time consuming, but it is the best way to ensure that the weld is free of any defects.
In addition to the above process, it is also important to use the right kind of welding rod or wire. Doing so will help to prevent overlap welding defects and will also help to ensure that the weld is strong and has a good appearance.
7. Burn-Through
Burn-Through is a common welding defect that occurs when too much heat is applied to the weld joint. This can result in excessive heat penetrating the base material, which can weaken the joint and potentially cause failure. Burn-Through is common in welding processes that require a high-heat input, such as TIG welding, MIG welding, and Stick welding.
The most common cause of Burn-Through is the lack of proper welding technique. Poor welding technique can lead to inadequate joint penetration, heat buildup, and inadequate shielding of the weld area. Inadequate shielding can lead to heat transfer to the base material. It can weaken the joint and create a potential for failure.
To reduce the risk of Burn-Through, the welder should make sure the weld is properly shielded and the welding material is of adequate quality. The welder should also use the appropriate welding voltage and the current setting for the type of welding material. It is also important to ensure that the weld joint is properly prepared. Finally, the welder should take the necessary precautions to prevent excessive heat buildup in the weld area.
In some cases, Burn-Through can be repaired. However, the repaired weld area should be inspected to ensure that it is of adequate quality. If Burn-Through is left unrepaired, it can lead to further weakening of the joint and potential failure.
Burn-Through is an important issue for welders to be aware of, as it can potentially lead to the failure of the weld joint. To reduce the risk of Burn-Through, welders should ensure that they are using the correct welding technique. By using proper techniques, welders can reduce the risk of Burn-Through and ensure that their weld joints are of adequate quality.
8. Distortion
Distortion is one of the most common external welding defects. It results from the thermal expansion and contraction of the welded parts. It can take the form of buckles, warping, and even stress fractures. And it can be a major hazard to the structural integrity of a welded piece.
Understanding the causes and effects of distortion is the key to preventing it. The two main contributors to distortion are the amount of heat and the weldment’s design and fabrication. Excessive heat can cause warpage, while poorly designed joints or weak welds can cause lipping or buckling. In addition, the weldment’s geometry and material properties, such as the coefficient of thermal expansion, can also affect the amount of distortion.
When it comes to preventing distortion, the key is to reduce the amount of heat used in the welding process. This can be done by using correct welding techniques such as preheating and post-weld heat treatment to reduce thermal stresses. The welding process should also be properly designed, taking into account the weldment’s geometry and material properties. In addition, the welding environment should be correctly set up, with the right shielding gas and arc voltage.
Additionally, it is important to inspect weldments regularly to check for any signs of distortion. Visual inspection is the most common method of detecting distortion. But ultrasonic testing can also be used to detect any internal cracks or flaws that may be causing the distortion.
In summary, distortion is one of the most common external welding defects. And its prevention requires proper welding techniques, design and fabrication of the weldment, and regular inspection. Understanding the causes and effects of distortion is key to preventing it. Ultimately it ensures the structural integrity of the weldment.
Internal Welding Defects:
Here, we are discussing some internal welding defects and their detail :
1. Slag Inclusion
Slag Inclusion occurs when molten slag becomes entrapped inside a weld during the welding process. It is a common internal welding defect that can lead to a range of problems. And it should be avoided as much as possible.
Slag Inclusion comes by a variety of factors including inadequate joint preparation, incorrect welding parameters, and uneven weld puddle control. It occurs when the molten slag is trapped between the base metal and the weld, creating a weak spot in the welded joint. Slag Inclusions can cause a variety of issues with the welded joint, such as brittleness, cracking, or porosity.
In order to avoid Slag Inclusion, it is important to take proper precautions during the welding process. Proper joint preparation is essential in order to ensure that the weld is free of any contaminants. It is also important to use the correct welding parameters and monitor the weld puddle closely. It ensures that it remains smooth and uniform.
Slag Inclusion can also be reduced by using a slag removal tool, such as a slag hammer or chipping hammer, to remove any entrapped slag from the weld. It is also important to use the correct type of flux and ensure that it is correctly applied. This will reduce the amount of slag that is created during the welding process.
Overall, Slag Inclusion is an internal welding defect that can lead to a variety of problems. It is important to take the necessary precautions during the welding process to ensure that slag Inclusion is avoided. And finally, the welded joint is of the highest quality.
2. Incomplete Penetration
Incomplete penetration is one of the most common internal defects that occur in welding. It is the result of inadequate metal fusion at the fusion boundary between two pieces of metal. This welding defect reduces the strength and integrity of the welded joint and can cause failure in applications requiring a strong bond. It can be difficult to detect, as it is hidden inside the welded joint.
Incomplete penetration is caused by a number of factors. The most common are improper joint design, inadequate joint preparation, incorrect welding technique, and incorrect welding parameters. Improper joint design can include incorrect joint fit-up, incorrect weld size, and incorrect joint preparation. Incorrect weld size can result in an insufficient amount of filler material which can lead to incomplete penetration.
Incorrect welding techniques can also contribute to incomplete penetration. It includes incorrect travel speed, incorrect electrode angle, and incorrect arc length. Incorrect welding parameters can include inadequate current, incorrect voltage, improper shielding gas, and incorrect polarity.
In addition to proper welding techniques and parameters, it is important to inspect welds for incomplete penetration. This can be done using either visual inspection or non-destructive testing methods such as X-ray or ultrasonic testing. Visual inspection may reveal cracks, porosity, or inadequate penetration at the weld joint. Non-destructive testing can detect welding flaws that are not visible to the naked eye.
Incomplete penetration can be a major problem if not addressed promptly. It can reduce the strength and integrity of the welded joint and can lead to failure in applications requiring a strong bond. By following proper welding techniques and parameters, adhering to the manufacturer’s recommended guidelines, and inspecting welds for incomplete penetration, the risk of this welding defect can be reduced.
3. Necklace Cracking
Welding is a process of joining two materials together, typically metals or thermoplastics, through the application of heat, pressure, and chemical reactivity. While welding is an incredibly efficient and reliable process, it is not without its flaws. One common defect, known as necklace cracking, can occur when two objects are welded together.
Necklace cracking is a type of internal weld metal defect. It occurs when the filler material between two pieces of metal does not fuse properly, leaving gaps or cracks in the weld. When this occurs, the weld is weakened and can potentially fail. It is often caused by improper preheating of the metal prior to welding or by using the wrong welding rod.
The most common symptom of necklace cracking is a visible defect in the weld. This defect is characterized by a pattern that resembles a necklace chain, hence the name. This pattern of cracks is caused by the weld metal being insufficiently melted, leaving gaps between the two pieces of metal. The gaps can be very small or large depending on the severity of the defect.
In addition to the visual defect, it can also cause the weld to become brittle and less able to withstand the pressures of welding. This can result in the weld failing under normal operating conditions. To avoid this, welders should always ensure that the metal is properly preheated prior to welding and that the correct welding rod is used.
Necklace cracking is a common internal welding defect that can be easily avoided. By following the appropriate welding procedures and using the correct welding rod, welders can reduce the risk of this defect occurring.
4. Incomplete Fusion
Internal welding defects such as incomplete fusion are common in welding processes, and they can lead to decreased strength of the weld joint. Incomplete fusion occurs when the base or filler material has not fused into the adjacent metal during the welding process. This causes the weld joint to have weak or nonexistent bonds between the metals, which can lead to cracking or other forms of failure.
Incomplete fusion can be caused by a variety of factors. For example, improper welding parameters, such as low heat input or incorrect travel speed, can result in incomplete fusion. In addition, inadequate cleaning of the workpiece can also contribute to incomplete fusion. Finally, improper preparation of the workpiece such as improper joint design or too small a root opening can also lead to incomplete fusion.
To minimize the risk of incomplete fusion, the welding process and parameters should be carefully set up and monitored. It is important to use the correct welding parameters and techniques to ensure that the heat input is sufficient to allow proper fusion. In addition, all workpieces should be clean and properly prepared, and any defects should be repaired before welding.
Incomplete fusion can be a serious problem, as it can lead to weakened welds that are prone to cracking, fatigue, and other forms of failure. To minimize the risk of incomplete fusion, it is important to properly set up and monitor the welding process, inspect welds for incomplete fusion, and to repair any defects before welding. By following these steps, the risk of incomplete fusion can be minimized and the quality of the weld joints can be ensured.
How To Prevent Welding Defects
Welding is an important process for joining two pieces of metal together in a strong and permanent bond. Unfortunately, if the welding process is not done correctly, it can lead to a variety of defects in the finished piece.
Common welding defects can include porosity, cracking, and warping, all of which can impact the structural integrity of the welded piece. To prevent welding defects, it is important that welders follow the best practices. This includes proper preparation of materials, selecting the right welding process for the job, and consistently monitoring.
Properly preparing materials is key to preventing welding defects. Surfaces should be clean and dry, and any rust or dirt should be removed before welding begins. It is also important to use the right materials and tools, as using a material of the wrong thickness or strength can affect the quality of the weld.
Selecting the right welding process is also important. Different types of welding processes are better suited for certain materials and jobs. Each welding process comes with its own set of instructions, which should be followed to ensure the best results.
It is also important to constantly monitor the welding process. Welders should check for any signs of errors, such as warping, cracking, or porosity. If any defects are noticed, the welding process should be stopped and the issue addressed before continuing.
Finally, welders should always use protective gear during the welding process, such as goggles and gloves. Its protect their eyes and skin from the intense heat and sparks that are produced during welding.
By following these practices, welders can ensure that their welds are strong and defect-free. With proper care and attention, welders can avoid common welding defects and create high-quality welds that last.
Conclusion
In conclusion, understanding the major welding defects is essential for the safety of welders and the quality of the products they produce. Knowing the different types of defects, their causes, and how to prevent them can help welders create better, safer welds with fewer mistakes. With this knowledge, welders can ensure that their welds are of the highest quality and that they are not wasting time, money, and materials due to poor welds.
If not corrected, welding flaws offer significant dangers that may result in disastrous situations. They can be costly and time-consuming to fix, but the cost of excellence is always worth it. Welders must comprehend the foundations of welding for this reason.
Welding procedures may now be carried out more effectively thanks to modern technologies. The execution and rectification of these flaws are always improving, along with a variety of testing techniques that enable the identification of various welding problems. Limiting weld flaws can be achieved by concentrating on improving both the equipment and technical skill. This encourages numerous industries to produce goods of unprecedented excellence which is truly amazing.
Related Article: Top 20 Best Welding Tools of 2024 for Welders
Related Article: Is Welding Hard? – The Ultimate Guide to Know About Welding
You may also read: The Ultimate Guide to Multi Process Welder


4 Comments
Pingback:
Pingback:
Pingback:
Pingback: